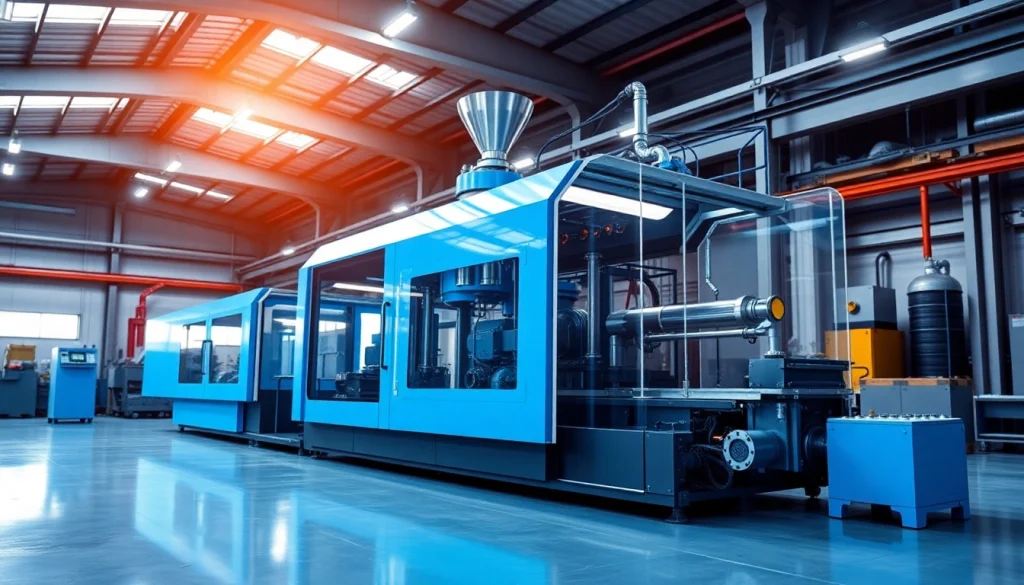
Understanding Blow Molding Technology
Blow molding technology has become a cornerstone in the production of plastic products, enabling businesses to manufacture everything from containers to intricate parts efficiently. This article delves deep into the various dimensions of blow molding, covering its fundamentals, the different types of machines available, and their applications across industries. As a notable Blow Molding Machine Manufacturer, focusing on the intricacies of this technology can help companies optimize their production processes effectively.
The Basics of Blow Molding
Blow molding is a manufacturing process for producing hollow plastic parts by inflating soft plastic into a mold. This technique utilizes thermoplastics and involves several key steps: material extrusion, mold formation, and cooling. The plastic is first heated until it becomes pliable and then stretched into a mold using air pressure, creating the desired shape. This process not only increases efficiency but also reduces material waste compared to other molding methods.
Types of Blow Molding Machines
There are three primary types of blow molding machines, each suited for different applications:
- Extrusion Blow Molding (EBM): This method involves extruding a tube of plastic, known as a parison, which is then inflated into the mold. EBM is ideal for producing large containers such as barrels and tanks.
- Injection Blow Molding (IBM): In this method, the plastic is first injected into a mold to form a preform, which is then transferred to another mold where air pressure blows it into its final shape. IBM is commonly used for creating smaller, more intricate bottles.
- Stretch Blow Molding (SBM): This technique involves stretching a preform to improve its material properties before blowing it into the mold. SBM is favored for producing high-strength and lightweight bottles.
Industry Applications for Blow Molding
Blow molding technology is widely used across many industries, including:
- Packaging: One of the largest applications includes producing bottles, jars, and containers for the food and beverage industry.
- Automotive: Components like fuel tanks and air ducts are frequently made using blow molding due to their lightweight and durable characteristics.
- Consumer Goods: Products like toys and household items often utilize blow-molded parts owing to their engaging designs and effective manufacturing processes.
The Importance of Selecting a Quality Manufacturer
Choosing the right blow molding machine manufacturer can significantly impact product quality and production efficiency. It is crucial for businesses to evaluate potential manufacturers thoroughly to ensure they align with their operational needs.
Evaluating Manufacturer Credentials
When assessing a blow molding machine manufacturer, companies should consider certification and industry accreditations. This includes ISO certifications, which indicate a commitment to quality and standards. Additionally, manufacturers with proven experience in the industry are likely to provide better support and innovation.
Customer Support and After-Sales Service
Exceptional customer support is vital, as issues may arise post-purchase that require immediate attention. Companies should inquire about the manufacturer’s support services, including the availability of spare parts, technical assistance, and warranty programs. A manufacturer committed to post-sale service ensures smoother operations and less downtime.
Case Studies of Successful Collaborations
Numerous case studies illustrate how businesses have benefited from choosing reputable blow molding machine manufacturers. For instance, a leading beverage company improved its production efficiency by 30% after switching to a supplier known for cutting-edge EBM technology. These success stories demonstrate the tangible benefits of selecting a capable manufacturer.
Key Features to Look for in a Blow Molding Machine
Not all blow molding machines are created equal. Here are some critical features every buyer should consider to maximize productivity and profitability.
Efficiency and Speed Considerations
Production efficiency is a determining factor when selecting a blow molding machine. Manufacturers should look for machines with optimized cycle times and high output rates. Some advanced machines offer capabilities exceeding 60,000 bottles per hour, greatly enhancing production capabilities.
Energy Consumption and Sustainability
With the increasing focus on sustainability, energy-efficient blow molding machines have become a priority. Manufacturers should consider machines that offer low energy consumption during production, reducing costs and environmental footprints. Options such as all-electric machines provide significant advantages in terms of energy efficiency and operational control.
Customizability and Design Flexibility
Blow molding machines that allow for rapid changeovers and custom options enhance operational flexibility. Being able to produce different sizes and shapes without extensive downtime improves productivity. Companies should choose manufacturers that offer machines with modular designs and versatile tooling options.
Comparing Leading Blow Molding Machine Manufacturers
With numerous players in the blow molding industry, businesses should conduct thorough comparisons to find the right partner for their needs.
Industry Leaders and Their Offerings
Companies like Uniloy, Wilmington Machinery, and Jomar Corporation are renowned in the blow molding sector. Uniloy stands out as a global leader offering four unique blow molding technologies alongside molds and associated tooling. Wilmington Machinery specializes in high-speed, multilayer extrusion systems, while Jomar is celebrated for its injection blow molding machines.
Customer Reviews and Testimonials
Customer feedback often provides invaluable insights into a manufacturer’s reliability and machine performance. Companies should seek testimonials and case studies highlighting successful partnerships, which can offer guidance and assurance in their decision-making process.
Price Comparisons and Value Analysis
Price is a significant factor but should not be the only one influencing decisions. Businesses need to conduct value analyses considering the machine’s lifespan, total cost of ownership, and potential return on investment. A lower-priced machine may not always be the best value if it compromises durability and performance.
Future Trends in Blow Molding Manufacturing
The blow molding industry is continuously evolving, driven by technological advancements and changing market dynamics. Understanding these trends can help manufacturers prepare for the future.
Technological Advancements on the Horizon
Innovations such as automation and connectivity through Industry 4.0 are reshaping how blow molding companies operate. The integration of smart technology in manufacturing processes allows for predictive maintenance, real-time monitoring, and enhanced production efficiency.
Shifts in Industry Demand and Production Needs
Consumer preferences are shifting towards more sustainable and lightweight packaging options. Manufacturers need to adapt by investing in technologies that focus on these emerging demands, ensuring they remain competitive in the evolving market landscape.
Preparing Your Business for Upcoming Changes
To stay ahead in the blow molding industry, businesses should prioritize continuous training for their workforce and embrace new technologies. Engaging with thought leaders and participating in industry conferences can provide insights into best practices and innovative solutions tailored for the future.